We all know that deforestation is the second leading cause of climate change but do we realise the fact that 17 trees are cut down to make 1 tonne of paper? If you translate it in practical terms, acres of land are deforested to collect wood for making pulp to meet the growing demand for paper!!! What makes handmade paper different is that it is made using materials like rags, etc. Thereby there is no fear of deforestation or global warming when you use handmade paper.
Dheyzo or Paper making is one of the thirteen traditional crafts of Bhutan going back several generations. In olden times, paper was mainly used in Budhist monasteries to write prayers, mantras , manuscript book etc.
Hand made paper or Dheshog is made from the bark of certain plants. The Daphne Papyri grown at an attitude of 1500 feet and below produces a strong, dark paper. The Edgeworthia Papyri found at higher altitudes of 3000 feet and above, produces a whiter, more fragile paper. Decorations on the paper are done with natural things like flowers, leaves, and fern leaves decorations on the paper.
Paper making is done without any environmental harm to the land, and without the use of chemicals. I visited the Jungshi handmade paper factory situated in Namtag Lam , which is 1 km from the main Thimbu town. Here I could watch the steps involved in the making of handmade paper.

- Step 1 β Collecting and drying of bark.
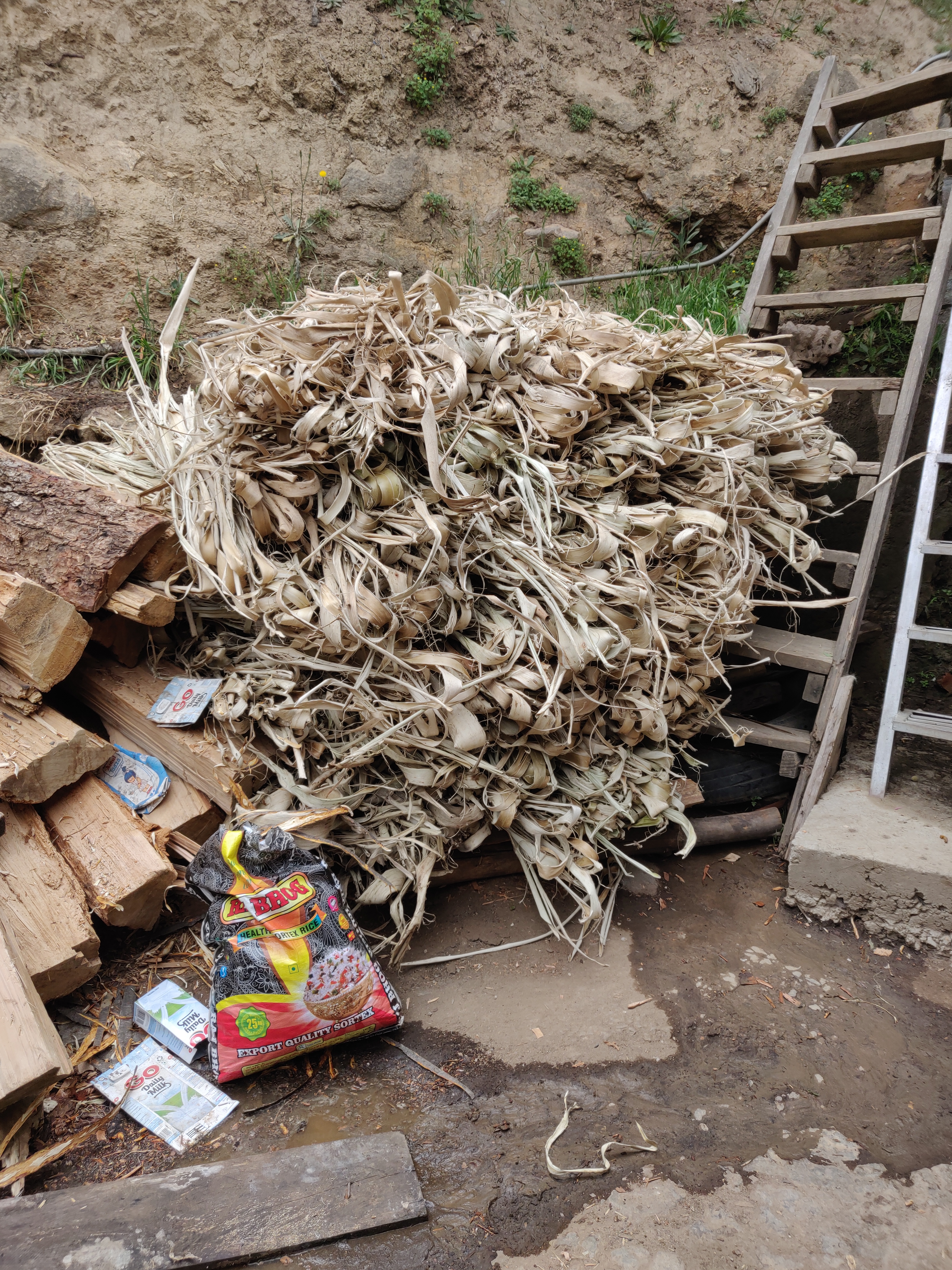
Step 2 β Soaking of bark
Strips of bark are soaked in water kept in large tanks for 24 hours.
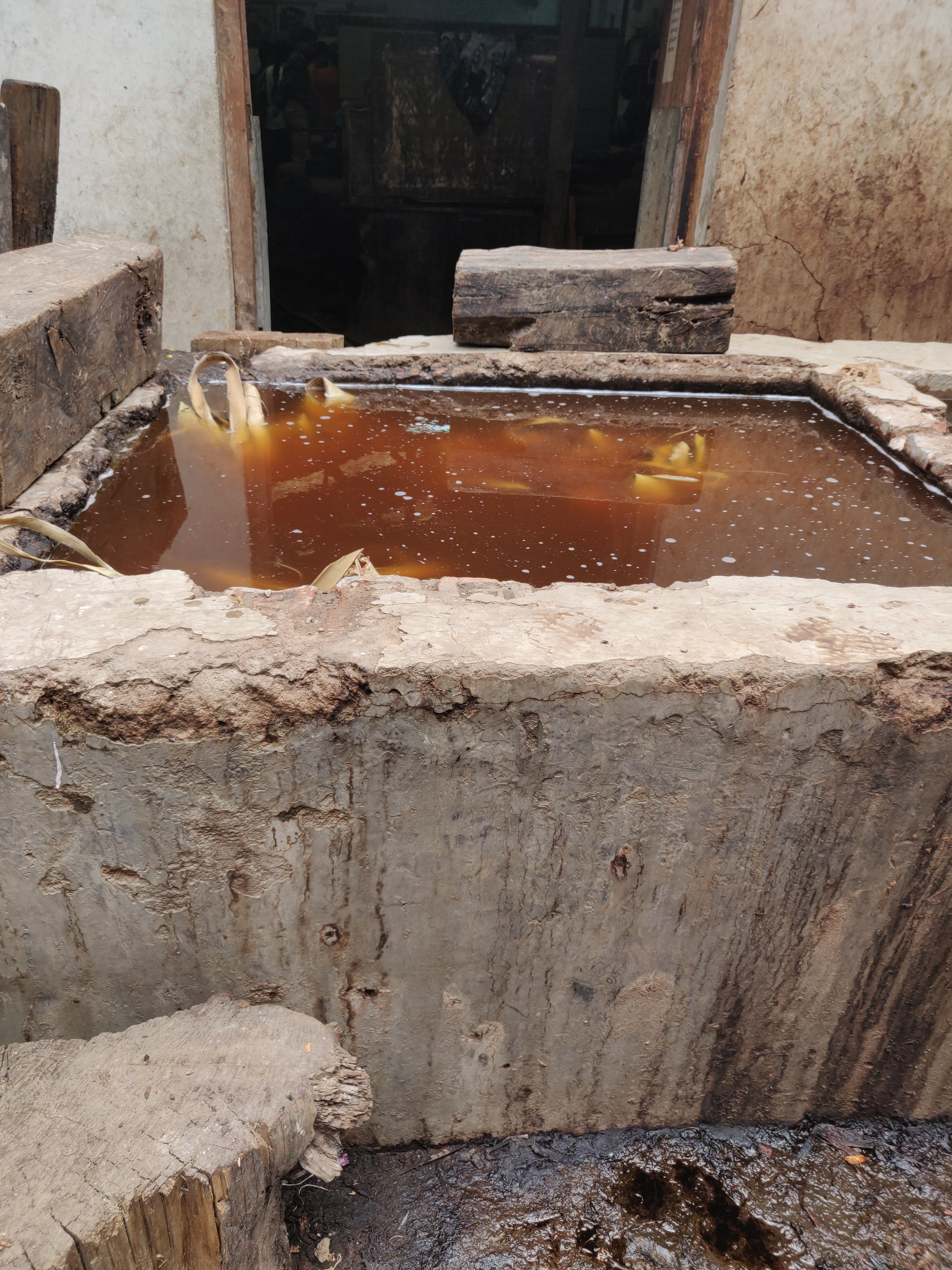
- Step 3 β Boiling of bark
It is then boiled in iron cauldrons over wood fire for one hour.
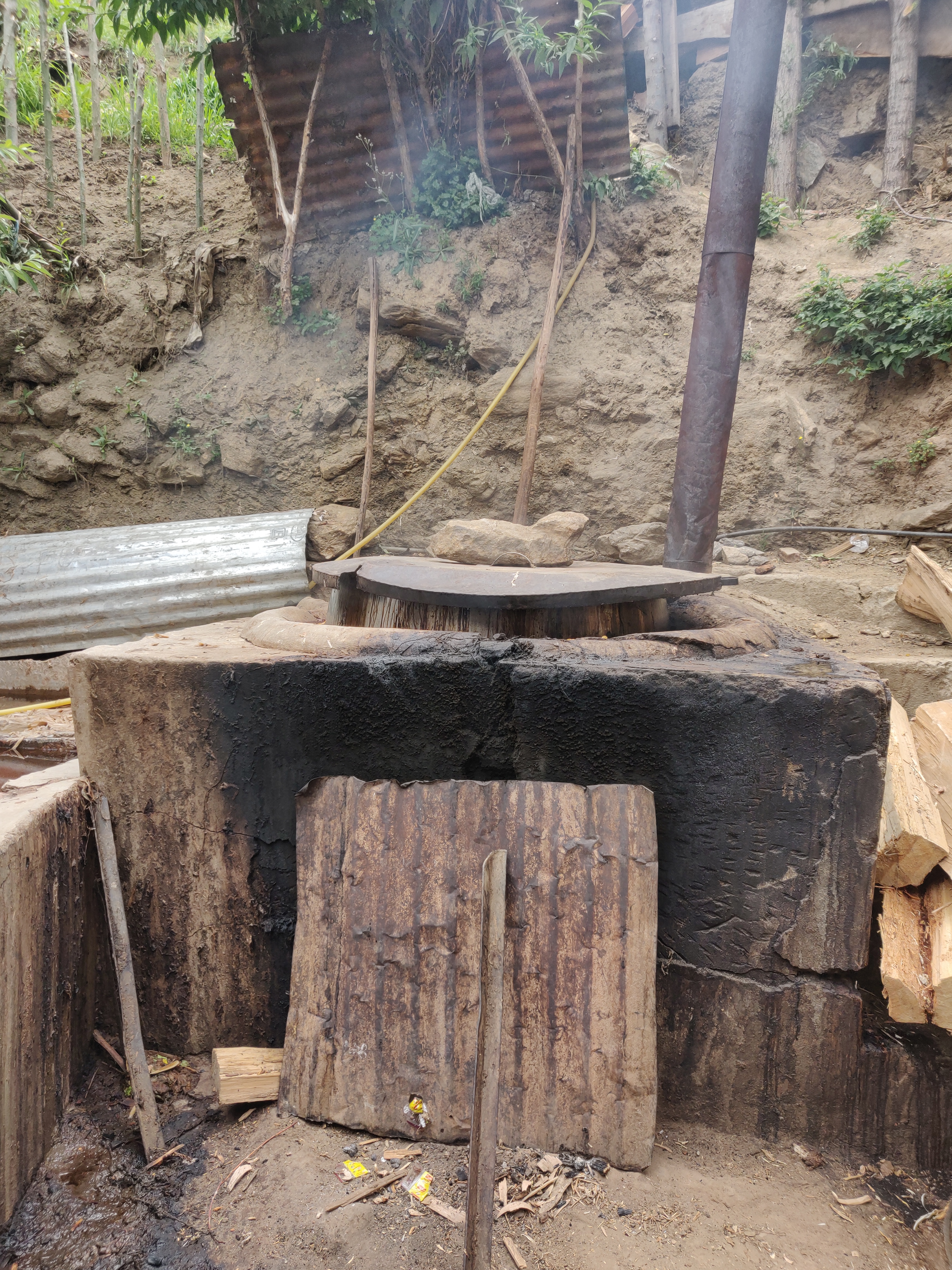
- Step 4 β Cleaning of bark
Boiled bark is washed thoroughly in clean water.

- Step 5 β Sorting of bark
Bark is then shredded and separated into three groups. First quality goes for making fine paper. Second quality goes for making paper for albums, journals etc. bark with dark colour etc are used to make rough paper.
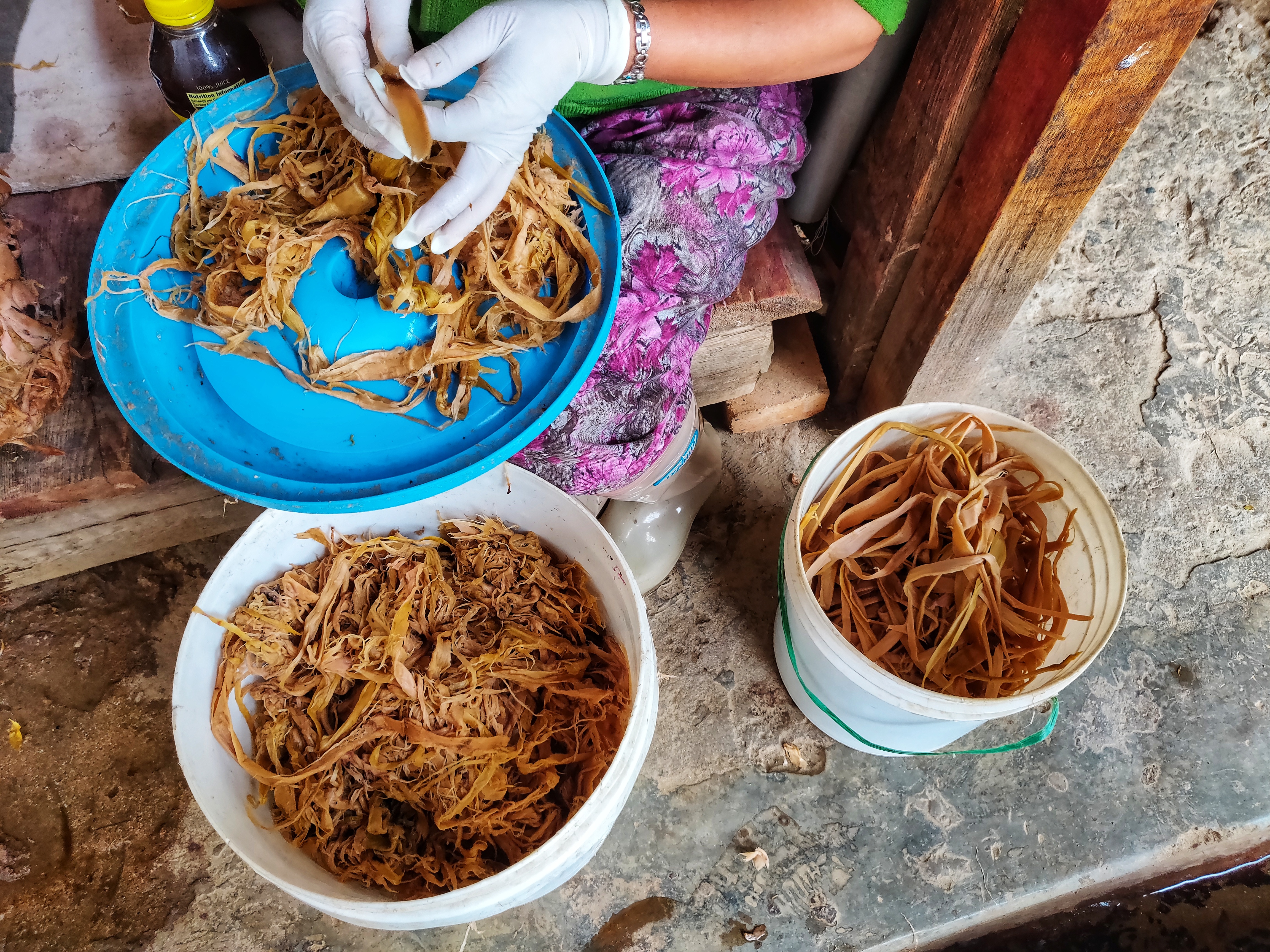
- Step 6 β Making of pulp
Bark is pounded by a machine to make fine pulp.

- Step 7 β Mixing of vegetable starch
Pulp is transferred to a large vat, where vegetable starch from hibiscus plant root is mixed.

- Step 8 β Swirling of bamboo filter
A wooden frame with a bamboo screen filter, approximately two feet by three feet in size, is dipped into the vat of the pulp and starch mixture. It is swished around to allow a thin layer of the mixture to spread out evenly over the screen
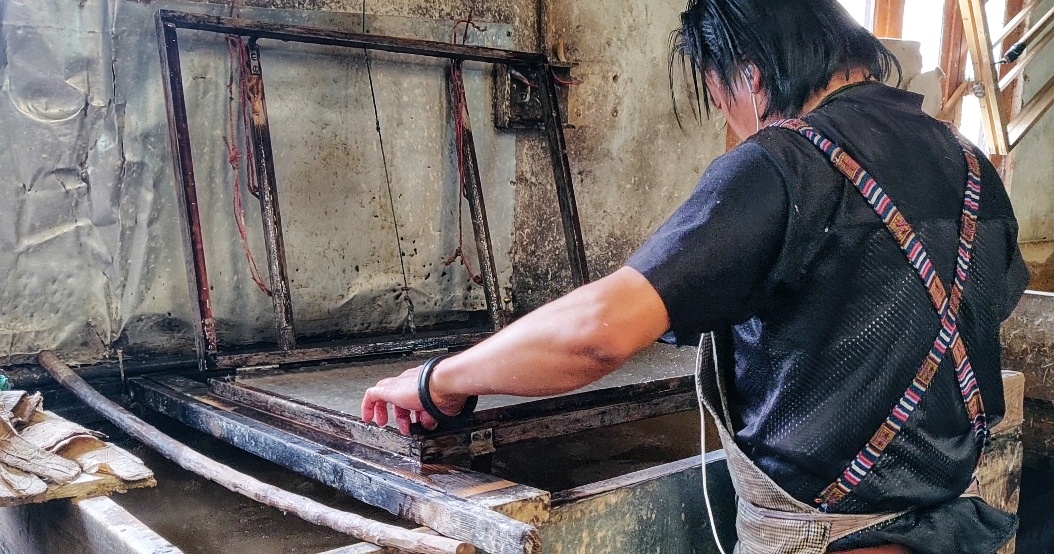
- Step 9 βFilter is taken out and paper is removed
Frame is opened and the bamboo screen over which a thin spread of pulp has formed is taken out from the wooden frame. The screen is carried from the vat to a table where a stack of paper has already been started. The screen is laid on top of the stack, and then carefully removed, leaving a new sheet of paper on top of previously made sheets of paper. This process is repeated over and over again, as many as 1500 times a day, by hand, creating a stack of paper, one sheet at a time.

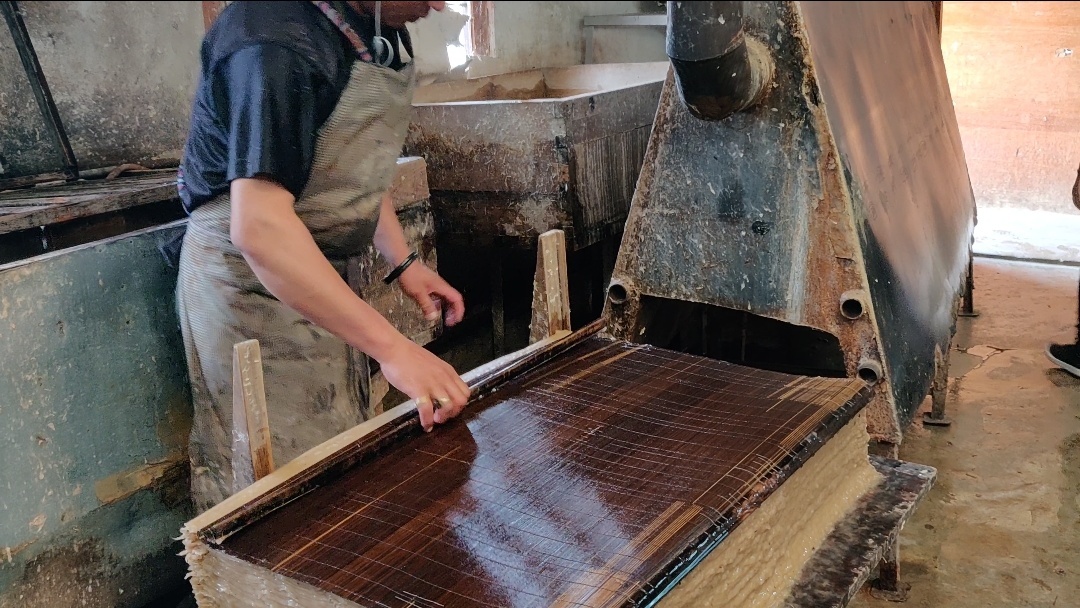
- Step 10 β Compressing paper
A whole stack of paper is then compressed to squeeze out any extra water.

- Step 11 β Drying
Each sheet of paper is taken off the stack, one by one, and is hung to dry on smooth vertical boards which are heated electrically. Some of the paper factories in Bhutan still dry the screens out in the sun.Thick paper takes 24 hours to dry while thin paper takes only one hour .

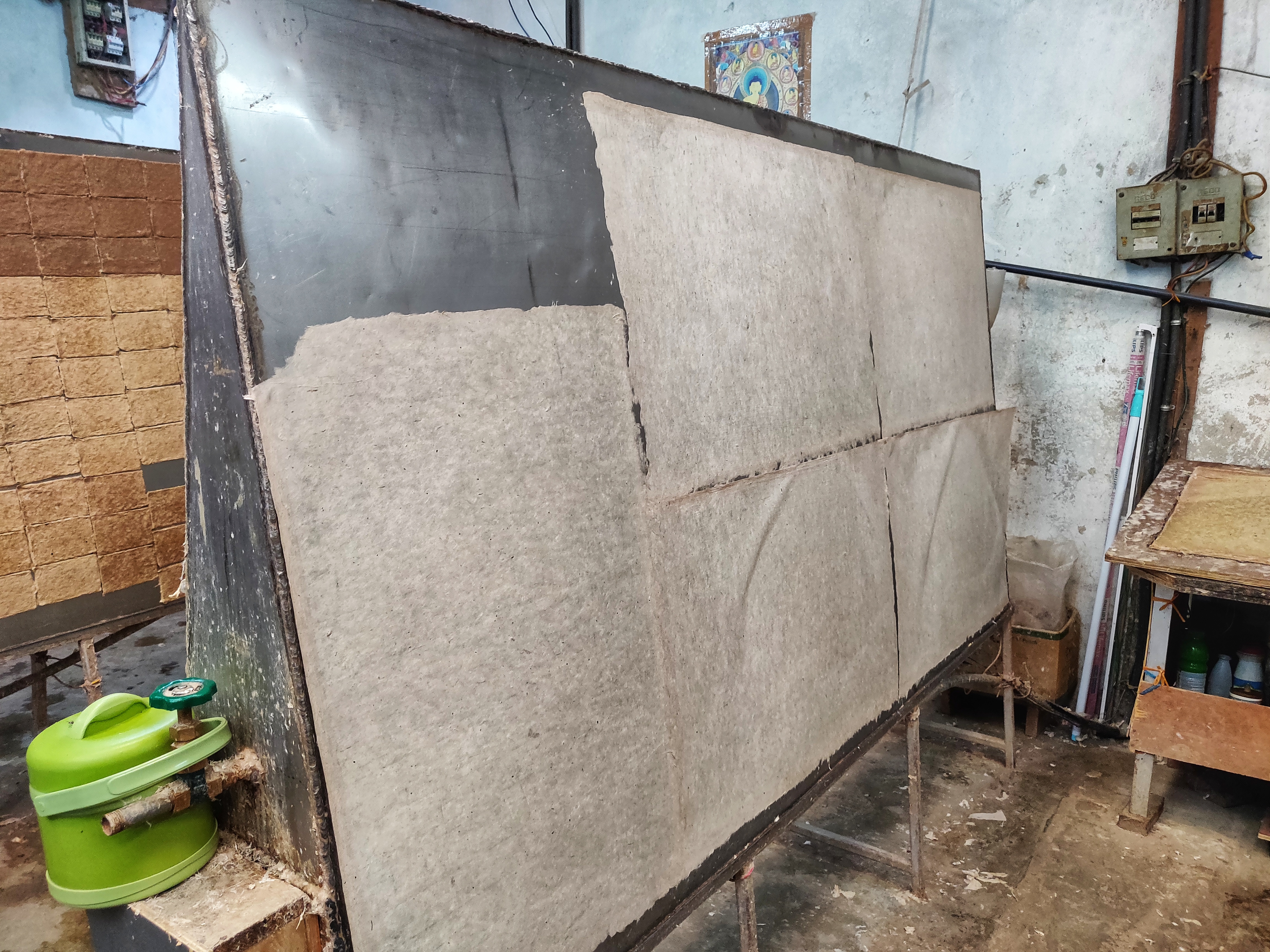
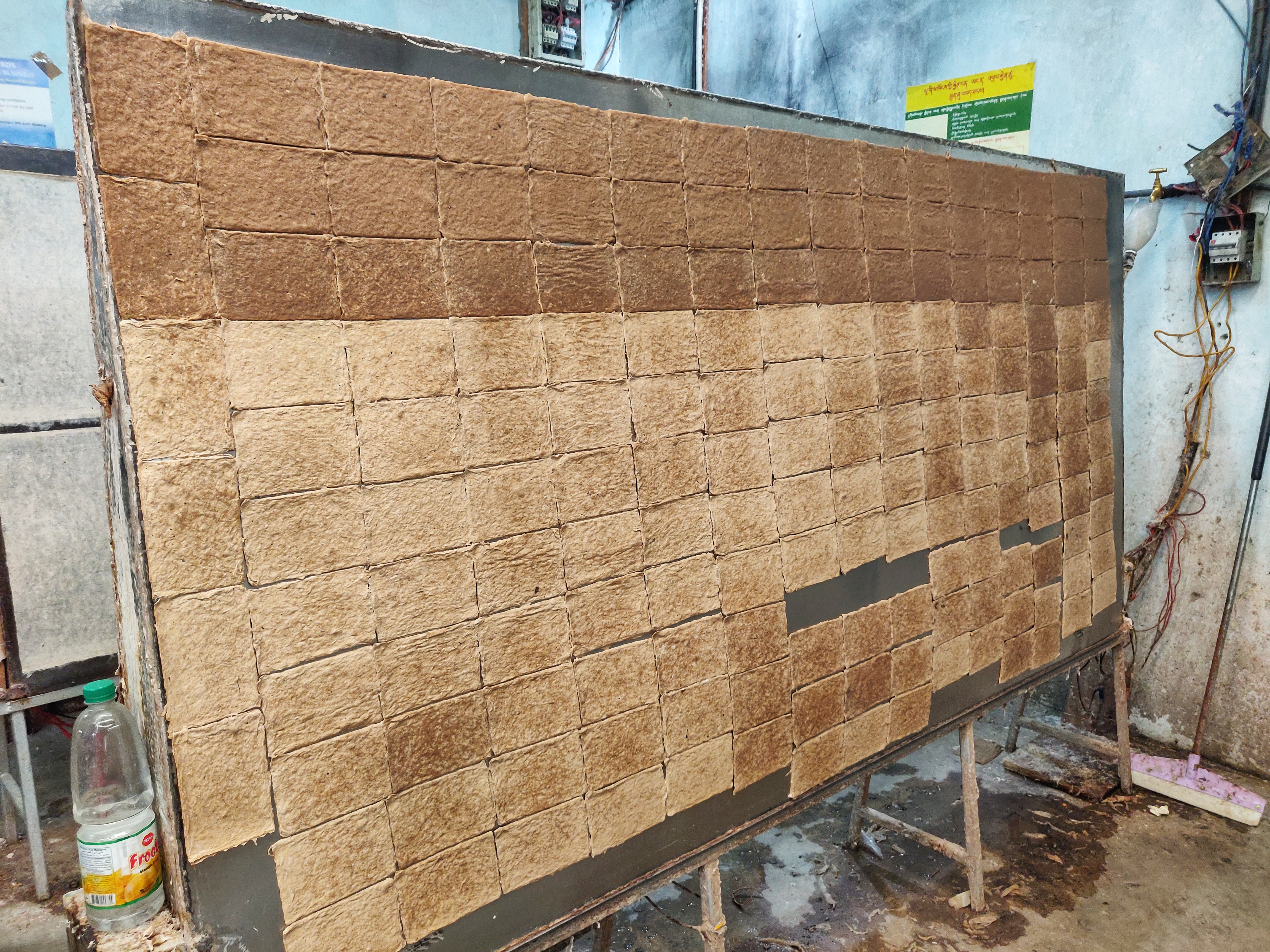
- Step 12 – Sheets are then coloured, painted etc. (Since photography of finished products is not permitted, following photographs have been taken from the FB page of Jungshi handmade paper factory)

- Step 13 – Some of the paper is cut into journals, glued into paper bags or shaped into lampshades. Other items that are made with handmade paper are greeting cards, envelopes, calendars, scrolls, wrapping paper, paper bags, and much more. Scrolls are decorated with Bhutanese symbols like dragons, monasteries, black neck crane, budha etc. All these are available in souvenir shops across Bhutan. Jhungshi paper factory has a small outlet attached to it that supposedly sells these items cheaper.


I could see the entire process of producing handmade paper using ancient traditional methods. It was like visiting a live museum! The time and effort put in for making each paper is highly appreciable. No wonder the paper was costlier than its machine made counterpart. After visiting the factory, I stopped complaining about the cost factor of handmade paper and started taking pride about the nature friendly nature of the chemical free paper. Next time, if you have a choice to buy handmade paper, do purchase it and support a noble cause.